Plastic rotational molding is one of the most important techniques for developing products in this material. If you are looking for a practical guide to understand and achieve the best results in plastic rotational molding, you are in the right place.
The guide will explore the benefits of rotomolding, its advantages, maintenance methods for machines, factors to consider when choosing the right machine, best practices, maintenance services, the importance of spare parts, and a comparison between types of rotational molding machines. Additionally, it will include information on productivity and preventive maintenance.
Plastic Rotational Molding
Plastic rotomolding is a process used to produce hollow objects, such as containers, boxes, and bins, from polymer powder. The machine designated for rotomolding uses a mold heated in a specific oven for this process.
The plastic rotomolding process begins with heating polymer powder in a rotomolding machine.
How is done
The plastic rotational molding process begins with heating polymer powder in a rotational molding machine. The powder is placed in a mold that will be placed in an oven, and the machine will be closed, so that the plastic can fill all the spaces of the mold. The rotational molding machine is then turned on, driving the material into the oven, so that the plastic melts into the mold. After this process, the plastic is left to solidify and then removed from the mold.

ROTOMOLDING UTILITY
A Rotomolding it stands out as a versatile technique in the manufacturing of hollow plastic objects, offering significant benefits. Its utility lies in the ability to effectively produce parts with complex and detailed shapes.
This method is particularly valuable in the creation of products such as fuel tanks, storage containers, toys, water tanks, and automotive parts.
The efficiency and flexibility of rotational molding make it the best choice in various industries, providing innovative and cost-effective design solutions for a variety of applications.
Benefits of Rotational Molding
Rotational molding is a very popular plastic molding process due to its simplicity and efficiency. It is a molding technique that allows for the production of much larger or more complex parts.
One of the main advantages is that the final product has excellent weather resistance due to being made of plastic, it has great wear resistance, and is resistant to corrosion.
Characteristics
Some unique characteristics of rotational molding enable the creation of customized parts, as the process allows for the production of different sizes and shapes. Rotational molding stands out for its production versatility, uniformity in part thickness, and the economic advantage due to the low cost in mold production, eliminating the need for high molding pressures.
Investment
Another benefit of rotational molding is that, with a significantly lower initial investment than other plastic molding techniques, it is possible to produce parts in large quantities in a short amount of time. Additionally, the rotational molding process is relatively clean, as it does not require the use of chemicals for production.
Advantages of Rotational Molding
Plastic rotational molding offers several advantages compared to other plastic molding methods. For instance, the rotational molding machine is more cost-effective than plastic injection. Additionally, rotational molding allows for the creation of strong and durable parts that are less prone to deformation or breakage.
Versatile process
Another advantage of plastic rotational molding is that the process is very versatile, allowing for the creation of parts in any shape, from small parts to large tanks. This means that it is possible to mold and create custom parts with specific shapes and sizes. Moreover, some machine models allow for mass production and repeatability.
Trends and Innovations for Rotational Molding
The rotational molding market has experienced some recent trends that may impact the industry in the coming years. Some of the main trends include:
More sustainable materials
Companies are increasingly concerned about sustainability; therefore, they are seeking more environmentally friendly materials for the production of rotomolded products. This includes the use of recycled, biodegradable, and renewable materials.
More advanced technologies
Rotational molding machines are becoming increasingly advanced, with features such as systems for temperature control more precision, automation, and real-time monitoring. This can enhance production efficiency and reduce operating costs.
Customization and flexibility
Customers are increasingly seeking more personalized products tailored to their specific needs. In other words, rotomolding companies are responding to this demand by providing more customization options and tailored production.
Automation
Automation is a growing trend in the rotational molding industry. The use of robots and automated loading and unloading systems can improve production efficiency and reduce machine downtime. This can also improve worker safety, reduce the chance of human errors, and increase the accuracy of the production process.
Quality control technologies
The use of advanced quality control technologies, such as computer vision systems and laser scanners, can ensure that rotomolded products meet the exact specifications of the customer and safety standards.
Use of sensors and Internet of Things (IoT)
The use of sensors and IoT technologies can help monitor the performance of rotational molding machines in real-time and detect issues before they occur. This can improve production efficiency and reduce maintenance costs.
How to Choose a Rotational Molding Machine
The Rotational Molding Machine is an essential equipment in the manufacturing of plastic parts, such as buckets, tanks, boxes, among others.
If you are looking for a rotational molding machine for industrial applications, whether for continuous use or limited quantity production, it is crucial to analyze some essential considerations before making the purchase.
Below, we list the main steps to follow when choosing a rotational molding machine::
1. Define application requirements:
The first step is to identify the specific requirements of your application.
The choice of the most suitable machine depends on crucial information such as the material to be molded, the shape of the parts, the daily or monthly production quantity, and the operating conditions.
2. Analysis of machine characteristics:
It is important to carefully analyze and evaluate the technical specifications of the machine, such as its size, production capacity, energy consumption, rotation speed, efficiency, versatility, etc.
3. Check the quality of materials:
It is important to check the quality of materials used in the construction of the rotational molding machine. The materials should be resistant to corrosion, high temperatures, and pressures.
4. Evaluate the cost-effectiveness:
Finally, it is necessary to evaluate the cost-benefit of the machine. It is important to consider the price of the machine, as well as maintenance costs. Moreover, it is important to consider the quality of the machine, its operating cost, and the technical support resources offered by the manufacturer.
Comparison between Different Types of Rotomolding Machines
Rotational molding is a complex but highly effective process for producing high-quality and designed parts. To achieve the best results, it is necessary to choose the right rotational molding machine that fits your production needs.
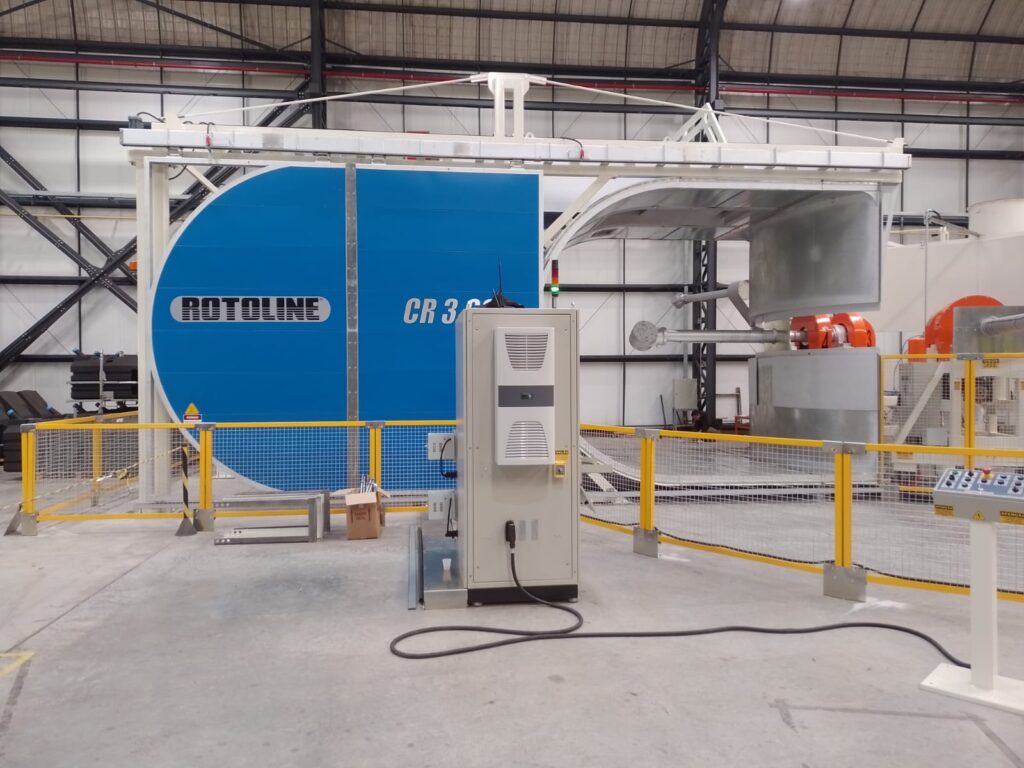
MACHINE MODELS
There are several different types of rotomolding machines used to create plastic parts. All of them are flexible and can be adapted according to project specifications. The most common rotomolding machine models include: Carrossel, Shuttle Machine, Laboratoryamong others.
Productivity in Rotomolding
There are several factors that must be considered to increase productivity in plastic rotomolding. productivity in plastic rotomolding..
One of the most important factors is the use of the correct rotomolding machine. Choosing the wrong machine can lead to rework, product failure, and delays in delivery times. The rotomolding machine must have sufficient capacity to handle project specifications. In addition, the cost of the machine should also be considered in the choice.
Correct use of rotational molding machines
Once the correct rotomolding machine is chosen, it is important to ensure that it is used correctly. To do this, it is necessary to train operators professionally so that they understand the rotomolding processes and are able to operate the rotomolding machine effectively.
Trainings
It is recommended that operators participate in regular training to keep their knowledge up to date.
Raw material
Another important factor to ensure the efficiency of rotomolding is the use high-quality raw materials. It is necessary to ensure that the raw material used is within the parameters specified by the project and that it is suitable for the rotomolding process. Low-quality raw materials can lead to defective products and process failures.
Choosing the Right Raw Material
The choice of the appropriate resin is a critical factor for the success of the rotomolding process. When choosing the best resin for rotomolding, it is important to consider some specific characteristics.
In addition to mechanical and chemical properties, it is crucial to evaluate the resin's flowability, melting temperature, impact and abrasion resistance, as well as shrinkage properties and pigmentation capacity.
The cost of resin is a crucial factor in the production of plastic parts, varying according to the type and quality of the chosen material. Balancing this cost with the quality and performance of the final piece is essential to ensure economic efficiency and meet industry standards.
This balance is vital, not only to optimize economic processes but also to ensure the production of excellent parts that meet rigorous industrial standards.
A thorough analysis of these elements contributes to informed and strategic decisions, directly impacting the quality and competitiveness of the final product.
ABOUT POLYETHYLENE
Among the various options available, polyethylene stands out as one of the most recommended resins for this process, due to its specific properties and characteristics.
Polyethylene is a versatile thermoplastic resin, widely used in rotomolding due to its ease of processing and its mechanical, chemical, and thermal properties that are ideal for this type of manufacturing.
Characteristics
It is highly resistant to impact, abrasion, chemicals, and weathering, making polyethylene rotomolded parts durable and long-lasting. Additionally, polyethylene has excellent corrosion resistance, which is particularly important in outdoor applications or aggressive environments.
Another advantage of polyethylene is its ability to mold parts with varying wall thicknesses. This allows for greater design flexibility and a wide range of applications.
Furthermore, it's important to mention that polyethylene is recyclable, which contributes significantly to the sustainability of the rotational molding process and enhances its environmental value.
The choice of the appropriate resin is a crucial factor in the rotational molding process. In other words, it is important to consider the specific characteristics of the resin and rely on a reliable supplier to ensure success in the production of high-quality rotomolded parts.
Spare Parts for Rotomolding Machines
Spare parts for rotomolding machines are essential to ensure the proper functioning of these machines and, consequently, the quality of the products manufactured. To ensure correct rotomolding, it is important to make sure that the spare parts are of excellent quality and properly calibrated.
Examples of spare parts that may be necessary over time:
- Molds
- Burners
- Thermocouples
- Valves
- Electrical parts
It is important to keep spare parts in stock to minimize machine downtime. It is recommended to contact the manufacturer of your rotomolding machine for more specific information about the recommended spare parts for your machine model.
The Importance of Molds in the Rotational Molding Process
As we've discussed before, rotational molding is a manufacturing process that involves heating a plastic material inside a hollow mold, which rotates on two perpendicular axes to evenly distribute the material and create a solid piece after cooling. In other words, the heating and cooling. In other words, molds play a crucial role in this process, ensuring the quality and precision of the final pieces.
Types of molds
There are different types of molds used in rotational molding. The most common are aluminum, carbon steel or stainless steel molds.
Aluminum molds
They are widely used due to their durability and heat dissipation capacity, which allows for faster and more efficient cooling of parts.
Carbon steel molds
In general, the cheapest and simplest handling material; however, not every piece can be made with it.
Stainless steel molds
They are ideal for producing parts with a smoother finish and are often used in applications that demand a high aesthetic standard.
CHARACTERISTICS OF THE MOLDS
The specifications of the final piece guide the design of the molds, which are developed to withstand the repetitive cycles of heating and cooling of the plastic material. This includes the rotation of the mold during the rotational molding process.
The geometry and design of the mold also directly influence the characteristics of the final part, such as wall thickness, material distribution, and mechanical strength.
MOLD QUALITY FOR ROTOMOLDING
Molds are essential for the rotational molding process as they are responsible for creating the shape and quality of the final parts. A well-designed and manufactured mold can ensure high-quality parts with precise dimensions and adequate mechanical properties. On the other hand, a poorly designed or manufactured mold can result in defective parts with irregular wall thickness, distortions, or other defects.
To achieve consistent and satisfactory results in the production of rotomolded parts, it is essential to invest in high-quality molds and ensure the correct design and fabrication of these.
Best Practices in Rotomolding Machine Operation
However, to enable higher quality and precision of products, it is necessary to operate the rotational molding machines correctly. Therefore, to achieve the best results, it is necessary to follow specific operational practices rotational molding machine operation practices.
Before starting the rotomolding process, check that the correct temperatures are regulated to avoid problems. Many rotomolding machines have both temperature control and flow control. Check that they are correct for safe operation.
Suggestions
- Ensure that the raw material is properly dried so that moisture does not accumulate inside the molds or in the rotomolding machine oven.
- Verify that safety devices, such as doors, are closed and locked.
- To prevent fires, it is essential to keep the area free from any combustible or flammable liquids.
- Check that there is sufficient pressure to maintain a consistent flow of air inside the machine.
- Check that all connections and valves are tight to prevent leaks. Check that electrical cables are properly connected to prevent electrical shocks.
- Ensure that all components are properly lubricated to prevent premature wear. Check that your safety equipment, such as masks and goggles, are properly adjusted for safe operation.
- Ensure that everyone has followed the safety procedures and that operators are fully aware of their duties and responsibilities.
Training for Rotomolding Machine Operation
To achieve quality results in plastic rotational molding, it is essential for rotational molding machine operators to receive training focused on the correct technologies and procedures. Additionally, the training should cover both basic machine operations and the proper use of molding materials.
In this guide, we will show the main steps to train rotomolding machine operators.
Before anything else, all operators should undergo a preliminary assessment. This assessment should check if the operators have the necessary skills to operate the rotational molding machine. After the assessment is completed, it is necessary to provide formal and dedicated training to the operators.
Important items
The training for rotomolding machine operation should include, first and foremost, basic instructions for safe use of the machine and proper use of molding materials. Operators should also understand the principles of plastic rotomolding, including fundamental elements such as temperature, pressure, and recipe time.
ASSESSMENTS
After completing basic training, it is important that operators are evaluated to analyze their performance and understanding of the operation. This evaluation should include a series of tests to verify the operators' skills in rotomolding machine operation, as well as their knowledge of rotomolding principles.
After completing the training and passing the assessment, the operators will be ready to operate the rotational molding machine safely and efficiently.
Maintenance for Rotomolding Machines
The quality of the manufactured products will depend on the execution of proper maintenance of the Rotational Molding Machine. Therefore, it is necessary to ensure that all components of the machine are in optimal operating conditions.
It is recommended to perform a check of the general conditions of the machine before starting the process. Therefore, check for any damaged components or any other issues that may affect the quality of the process.
MECHANICAL COMPONENTS
Additionally, it is important to check if the mechanical components of the machine are properly lubricated. The appropriate oil should be used to prevent future issues. It is also important to ensure that the machine components are clean and free from dirt.
Oven
During the rotomolding process, it is necessary to check the oven temperature. The ideal temperature depends on the type of material being molded. Moreover, it is crucial to ensure that the temperature control system is fully operational.
Finally, it is important to check for any air or vacuum leaks in the rotomolding machine components to avoid process issues. Proper calibration of the vacuum system is also fundamental to guarantee the quality of the manufactured products.
How to perform Preventive Maintenance on Rotomolding Machines
Preventive Maintenance
Preventive maintenance is one of the most important stages of the rotomolding process. This stage ensures that the rotomolding machine operates correctly and efficiently, with minimal interruptions and failures.
For preventive maintenance, it is necessary to periodically perform and review various steps to ensure the machine's maximum performance.
First step
It involves the periodic inspection and cleaning of machine parts. Cleaning should be done carefully to avoid damaging any part of the machine.
Second step
Involves inspecting the machine parts to check if any part is worn out or damaged. The most commonly inspected parts include the heating system, valves, and hoses.
Third step
Check if all parameters are working correctly; these parameters include temperature, pressure, power, and speed. Therefore, it is necessary to record any changes in parameters to verify if the machine is functioning properly.
Fourth step
To test the machine to check if the rotomolded product is being produced according to the specifications.
Maintenance
A plastic rotomolding machine is a crucial equipment for producing many products. Therefore, it is essential to maintain the machine in good working condition and adopt safety measures to ensure it can perform its functions effectively and safely.
There are some basic services you can consider to keep your rotomolding machine in excellent condition:
1. Inspection and preventive maintenance
Experienced technicians should periodically conduct an inspection to assess compliance with safety standards. This task should include checking all machine elements, as well as ensuring the machine functions align with the needs of the production process.
2. Corrective maintenance
If there are issues with the machine, technicians can also assess and repair them.
In such cases, it is important to check if the supplier provides the necessary spare parts and if there are suitable tools for performing maintenance.
3. Technical Support
The machine supplier must offer a service Technical Support to clarify any potential doubts. Additionally, it is ideal to have customer support service to assist in diagnosing and resolving technical issues, ensuring the proper functioning of the machine.
Conclusion
In summary, this guide has presented to you the main trends, benefits, and best practices of plastic rotomolding.
It has also offered information to help you choose the right equipment, identify the main spare parts components, and the training required to operate the rotomolding machines.
Finally, it has provided some tips and information about maintenance and technical assistance services, as well as preventive maintenance to provide good performance over time.
Therefore, rotomolding can be a good option for plastic manufacturers who want an efficient and productive process to produce quality plastic products.