Having the right moulds for rotomolding is essential for manufacturing any plastic product. The quality, precision, durability, and resistance to corrosion of the produced parts depend on the moulds. To ensure the best performance in the manufacturing process, it is important to understand the different types of moulds and their specific characteristics.
In this article, we will look at what rotomolding is, the importance of choosing the best moulds, the different types of moulds, mould design, maintenance and repair of moulds, and the recent trends in rotomolding mould technology.
WHAT IS Rotomolding?
A Rotomolding is a popular process for manufacturing plastic parts, which involves using moulds to produce items in complex and specialized shapes. The process uses plastic pellets, which are heated, melted, spread, and extracted from the moulds. This molding technique is ideal for working with polyethylene, ranging from basic parts to highly specialized materials.
Rotomolding is frequently used in the production of rotomolded, sanitary articles, agricultural equipment, fuel tanks, water reservoirs, and others.
The rotomolding process has become particularly popular among plastic manufacturers due to reduced manufacturing costs. This is because most products can be produced in smaller batches or in large quantities, depending on the machine model used.
Rotomolding molds play a crucial role in defining the shape of the piece to be manufactured. We manufacture these molds from steel, aluminum, or other materials, depending on the design of the piece to be produced.
A THE IMPORTANCE OF CHOOSING THE BEST MOULDS
Choosing a good mould for rotomolding is the first step to ensure the success of your project. It is, therefore, crucial to be aware of some important factors when choosing the best mould:
MOULD DESIGN FOR ROTOMOLDING
The mould design needs to be accurate to ensure precise and efficient molding cavities. The mould design should also ensure that the internal surfaces are smooth and free from streaks, as this will reduce leakage problems in the rotomolding process.
MOULD MATERIAL TYPE
Additionally, it is important to choose the correct material for the mold. Rotomolding molds are typically manufactured in different metals or metal alloys. When selecting a mold, it is essential to consider this item with great attention, as each material has its own characteristics and properties. The most common materials used for molds include steel, aluminum, zinc alloy, and stainless steel.
COST
Finally, the cost of the mould should also be considered when choosing a mould for rotomolding. Costs vary according to the chosen material, the size of the mould, and the complexity level of the project. It is important to understand that the price of a rotomolding mould project is directly proportional to the quality of the final product. Therefore, it is advisable to invest in a quality mould to ensure that the final product is of high quality and durable.
TYPES OF MOULDS FOR ROTOMOLDING
The mold is one of the most important parts of rotational molding. The shape, size, and final design of the finished product are determined through it. Therefore, it is crucial to understand the different types of molds to select those that best suit production needs.
Rotomolding molds are commonly manufactured in cast iron, steel, stainless steel, aluminum, or other materials resistant to high temperatures. Each material has its own characteristics that should be considered when choosing the appropriate material.
MOULD STRUCTURE
Regarding the structure, rotomolding molds usually consist of two parts. The first part gives the desired shape to the final product, while the second part serves as support to keep the first part assembled. The mold can contain one or several cavities, depending on the type of product to be manufactured, contributing to the diversity of shapes available in rotational molding.
In addition to the material and design of the mould, another vital detail is the external finish. The finish can be smooth or rough, depending on the desired final product, and the quality of the finish is one of the characteristics that define the quality of rotomolding. Therefore, it is essential to select the right materials and processes to ensure the desired finish.
DESIGN MOULD
Choosing the best mould design for rotomolding is crucial for the success of a product of this nature. It is essential that those responsible for the design take into account the technical limitations of rotomolding. Since the finished part must fit inside the mould, the mould design must include all the features of the desired product.
HOW TO DEFINE MOULD DESIGNS FOR ROTOMOLDING?
The first step in manufacturing a mould for rotomolding is choosing the material for the mould. It is recommended to use steel or other heat-resistant material, as rotomolding requires high temperatures.
Steel moulds allow the production of a wide variety of high-performance parts. Aluminum moulds, on the other hand, are lighter, cheaper, and can also withstand rotomolding temperatures.
When designing a mold for rotational molding, it is crucial to take into consideration the desired characteristics of the final product. For instance, the thickness of the walls is important to provide stability and strength.
The size of the mold must be taken into consideration since it is often necessary to have a larger or smaller mold to produce pieces in specific sizes. Additionally, the mold size must be compatible with the size of the machine used to rotomold the parts. Finally, the type of coating used for the mould can also affect the finish and durability of the rotomolded part.
ASSEMBLY AND FIXATION OF MOULDS
The assembly/fixation of the moulds is done on arm The size of the mold must be taken into consideration since it is often necessary to have a larger or smaller mold to produce pieces in specific sizes. Additionally, the mold size must be compatible with the size of the rotational molding machine. In larger molds, assembly and fixation can be carried out using screws or simple fixation systems, for example.
FOR SMALL PARTS:
If the intention is to use several small or medium-sized moulds, it is very common to use spiders. The Spiders funcionam como uma rede na qual vários moldes podem ser fixados por meio de parafusos ou outro sistema de fixação.
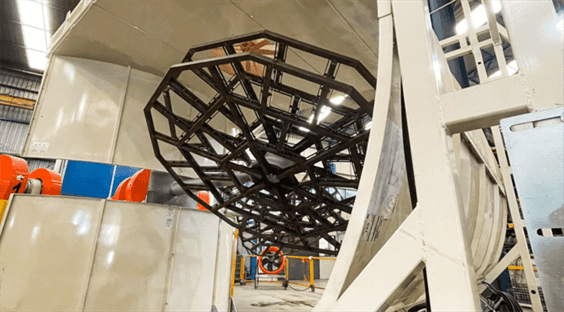
MAINTENANCE AND REPAIR OF MOULDS FOR ROTOMOLDING
Maintenance and repair of moulds are essential parts of the rotomolding process, as they are exposed to daily damage due to high temperature, pressure, and abrasion during the casting process.
To ensure that products manufactured with the moulds are consistent and of quality, it is necessary to perform maintenance and repairs periodically using the highest quality standards.
WHAT TO EVALUATE IN MAINTENANCE?
Maintenance of the molds should include cleaning and grinding of the internal channels, checking for defects on the internal and external surfaces of the mold. The main goal of maintenance is to prevent issues during the manufacturing process of the products. It is also crucial to conduct a thorough inspection of all mold details to identify possible failures or damages resulting from continuous use.
Trained and experienced professionals should perform all repairs on the molds to ensure maximum safety in the manufacturing process, as well as the best quality of the final product. Additionally, some materials can only be repaired through chemical or thermal means due to their high tolerated temperature. The most common methods for repair are TIG (Tungsten Inert Gas) welding and MIG (Metal Inert Gas) welding.
Maintenance for improvements of moulds for rotomolding
In addition to traditional repairs, it is possible to make improvements to the moulds to enhance the final characteristics of the manufactured product. For example, you can make improvements to the overall shape of the mould to reinforce strength and reduce the chances of failure during the process. These modifications to the designs also allow for greater accuracy in mass production of the finished product.
TRENDS IN TECHNOLOGY OF MOULDS FOR ROTOMOLDING
Currently, the technology for rotomolding molds is constantly evolving.
Mold technology plays a crucial role in the rotomolding process, being essential to ensure high-quality results. There are some trends that are enabling companies to improve their productivity and quality.
3D DESIGNS
One of the main trends is the adoption of 3D software to design and produce moulds quickly and easily. 3D software can create precise models of the desired moulds, meaning that the manufacturing process becomes faster, simpler, and less challenging. Furthermore, 3D designs can be standardized to facilitate the reproduction of the necessary moulds.
RAPID PROTOTYPING
Another significant trend is the use of rapid prototyping (RP) to create prototypes and test moulds before mass production. This is because RP can provide companies with a quicker return on their investments than using traditional processes in the rotomolding industry.
OTHER TRENDS
In addition, there are other modern trends regarding rotomolding mould technology, such as CNC machining (Computer Numerical Control), CAD/CAM (Computer-Aided Design/Computer-Aided Manufacturing) processing, and laser machining. These advanced techniques have enabled companies to produce more complex moulds in a simpler way than ever before.
Due to the advanced molding technologies available today, companies can not only save money in the short term but also achieve better long-term results due to the rapid and reliable production of the final products.
Conclusion
After a quick analysis, we realize that choosing the best moulds for rotomolding is essential for several reasons. It is important to consider the different types of available moulds, as well as the emerging trends in the industry. Additionally, maintenance and repair of the moulds are also critical to ensure that the moulds function correctly.
By adopting appropriate designs, properly determining your needs, and implementing maintenance and repair programs, companies can benefit from the rotomolding process to create quality products.