When it comes to productivity in rotational molding, it is important to recognize that each step of the process plays a crucial role in achieving the best results. A significant error in any of these steps can render all your other efforts useless. Fortunately, there are some productivity tips you can use to enhance the quality and production efficiency of rotational molding.
What you will find
In this article, we will present eight steps you can take to increase productivity productivity in rotational molding, including selecting the right equipment, optimizing cycle time, automating processes, efficient production management, implementing preventive maintenance, monitoring and controlling quality, training and qualifying employees, performing data analysis, designing products, and investing in new technologies.
Choosing the correct machine
One of the key productivity tips in rotational molding is selecting the right machine. The machine used for rotational molding needs to have the appropriate precision to ensure high-quality products. Additionally, it should be capable of operating at high production rates.
What to consider before purchasing a rotational molding machine?
When choosing the right machine, there are some important considerations to keep in mind:
Machine structure
É importante construir a máquina com materiais resistentes para garantir que ela molde os produtos facilmente. Ou seja, uma boa máquina de rotomoldagem deve ter boa resistência ao desgaste e ter peças de alta qualidade.
Mold type
Choosing the appropriate mold type for rotational molding is important.
Automation level
It is important to choose a rotational molding machine that is also automated. This will help ensure a high level of production and also keep the production time as short as possible.
Price
The price of the rotational molding machine is also an important aspect to consider. It should be affordable and fit within the company's budget.
Optimization of cycle time
Optimizing cycle time is one of the key productivity tips in rotational molding. Cycle time refers to the total interval between the start and end of a process cycle. It is possible to reduce cycle time by implementing various appropriate techniques.
Oven time
One of these techniques is reducing oven time. By reducing oven time, the heating and molding time is decreased, allowing the product to be released from the machine more quickly
This, in turn, leads to lower production costs as less energy is consumed. A useful tip is to maintain the machine's temperature consistently during both the molding and cooling phases.
To improve oven time, it is necessary to understand and evaluate your production process in order to adjust the recipe according to your needs.
Material quality
Another way to optimize cycle time is by improving the quality of the material. Enhancing material quality means reducing the occurrence of defects and increasing durability, resulting in enhancing productivity productivity. A helpful tip here is to use high-quality materials and regularly monitor qualification parameters.
Training
Furthermore, it is essential for rotational molding operators to have knowledge of both the process and the machine. Process knowledge helps identify issues and improve parameters, while machine knowledge is crucial for adjusting machine settings to achieve desired results. This optimization of the process time leads to increased productivity.
Process automation
One of the primary strategies for increase productivity in rotational molding is process automation. By automating production, rotational molding can be performed more efficiently, saving time and resources.
There are several ways to automate the rotational molding process, ranging from using modern machines to implementing intelligent algorithms to optimize production.
Machine programming
Another example of automation is task programming, which allows the machine to complete rotational molding more efficiently and at lower costs. For instance, a common use of automation is programming the machine to perform specific steps of the molding process, thereby reducing production time.
Accessories that facilitate day-to-day operations
Furthermore, it is possible to acquire rotational molding machines with accessories that enhance automation, such as automatic weighing scales, direct mold feeding, automatic mold opening and closingamong others.
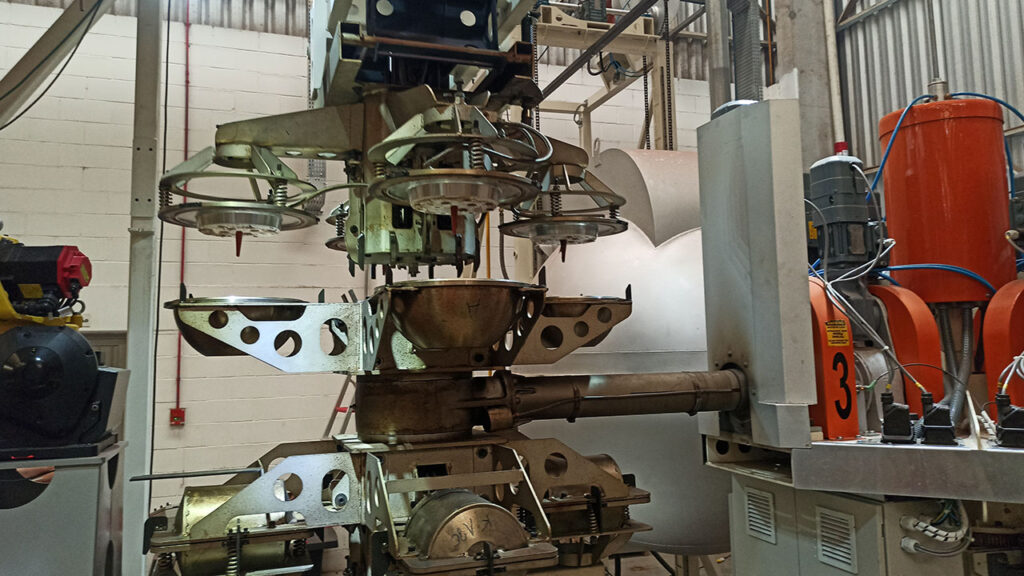
These items can save time and increase productivity in your rotational molding parts manufacturing process.
Efficient production management
Efficient production management is crucial for the success of the rotational molding industry. With the increasing demand for rotational molded products, it is essential to adopt tools and strategies that optimize the production process and ensure the quality of the final products. Here are some ways to increase productivity with efficient management:
Process automation
Automation is one of the key tools that can contribute to increased productivity in rotational molding. Automated systems for mold loading, temperature control, and cycle times can enhance efficiency and reduce human errors.
Production management software
Using specialized software to manage the entire production flow is essential for efficient management and, consequently, increased productivity. These tools allow for detailed planning, inventory control, traceability, and monitoring of production line performance.
Data analysis and performance indicators
Data collection and analysis are fundamental to identify bottlenecks, areas for improvement, and optimization opportunities in rotational molding. Tools such as Overall Equipment Efficiency (OEE) enable the measurement of equipment effectiveness and identification of areas that need improvement.
Lean Manufacturing
The Lean philosophy is widely applied in the rotational molding industry to eliminate waste and optimize processes. The use of tools such as value stream mapping, 5S, and Kanban helps identify and eliminate non-value-added activities in the production process.
Training and team empowerment
Efficient production management also involves investing in team development. Training on best practices in rotational molding, preventive maintenance, and workplace safety is crucial to ensure the quality and efficiency of the production process.
Preventive maintenance
Preventive maintenance is the key to success in rotational molding. Regularly evaluating the machine and the quality of the finished product, along with performing periodic maintenance, helps ensure optimal rotational molding performance and increased productivity.
Before starting production, all parts of the rotational molding machine should be carefully inspected. Check for risks, natural wear, cracks, and other forms of degradation. It is essential to regularly inspect the wheels, joints, fittings, and recommended maximum limits to avoid waste and delays.
Seek services from specialized technicians on the best way to monitor and adjust the machine. This way, you can improve machine performance, minimize material waste, and increase productivity.
Monitoring and Quality Control
Monitoring and quality control are fundamental for the success of productivity in rotational molding. Rotational molding with failures, defects, or imperfections inevitably reduces production yield. Therefore, it is important to implement monitoring and quality control techniques to maintain the quality of produced items at an acceptable level.
One of the key productivity tips tips in rotomolding is to create a monitoring scheme for items such as production, quality, safety, costs, and other key variables involved in the production process.
A monitoring system can help identify irregularities and trends, as well as assist in data-driven decision-making.
Quality Control Plan
Creating a quality control plan is also essential to ensure quality and productivity. The quality control plan should include inspection procedures, testing, and quality analysis.
Procedures should be applied at all stages of the rotomolding process, from material preparation to the delivery of the final product.
Data Analysis
Furthermore, it is advisable to adopt data analysis methods to track the quality of the rotomolding process. This approach allows identifying quality issues in the produced items, as well as detecting trends that can lead to productivity improvements..
Finally, it's important to remember that you should regularly review monitoring and quality control as continuous processes to ensure the quality and productivity of rotational molding.
Training and team empowerment
One of the most important factors to increase productivity in rotational molding, training and development of the workforce are crucial. Trained individuals with knowledge are required to carry out the complex rotational molding procedure efficiently.
Therefore, it is important to provide proper training to operators, ensuring they are aware of the necessary processes and tools. The training should include information on safety, equipment handling, machine installation and configuration, as well as basic knowledge about rotomolding itself. One suggestion is to seek training from the rotomolding machine supplier.
Encourage the Pursuit of Knowledge
Furthermore, it is important to encourage the team to seek continuous improvements. For example, employees can be encouraged to seek productivity tips in rotomolding and share knowledge. This will help the team maintain a high level of productivity and quality.
Provide Feedback
Finally, it is important to provide regular feedback and encourage continuous improvement. Providing support to team members is a great way to increase productivity in rotomolding. Feedback should be proactive and timely, allowing the team to quickly address potential issues and improve their work practices.
Data Analysis
Analyzing the collected data is one of the most important steps in improving productivity in rotomolding. By keeping records and monitoring trends, manufacturers can identify key issues that cause production delays. This data analysis can also identify areas for improvement in processes and develop productivity tips productivity tips to increase production.
Identify Bottlenecks
As a first step in data analysis, it is important to identify the main bottlenecks. These points are usually the slowest in the process. The team can use data analysis tools to see what triggers the delays.
Perform Performance Analysis
With this information in hand, the next step is performance analysis. This analysis compares the productivity results of rotational molding with the established objectives. By comparing these data, it is possible to easily identify areas that need adjustments for improving productivity.
Identify Trends
In addition to performance analysis, data can also be used to identify trends that may impact rotomolding. For example, if the data shows that materials are wearing out more quickly, the team can use this information to develop a solution to increase material durability.
Data analysis can also help manufacturers identify and address safety issues. For example, if the data shows that the machine temperature is too high, the team can take measures to reduce the risk of accidents.
Product Design
When it comes to increase productivity in rotomolding, it is important for product designs to be well-established before the process begins. This means developing the design with care and dedication to achieve the best possible results. For this, there are some important tips to keep in mind:
Learn material and process specifications
Before starting to develop products for rotomolding, it is important to understand the limitations of materials and processes so that the product is as efficient as possible.
Use 3D design tools
The use of 3D design tools makes the product development process easier and increases productivity. Additionally, these tools allow you to visualize the design before sending it for rotational molding, reducing errors and production costs.
Understand customer needs
It is important to know the requirements and desires of customers to ensure that the final product is exactly what they are looking for. This way, it is possible to develop a product that meets all the needs and can be efficiently produced with rotomolding.
Perform testing before production
Conducting tests before production allows for an analysis of compliance with requirements and the product's ability to meet customer needs. Additionally, testing prototypes before production helps minimize issues and errors during the rotational molding process.
Investments in New Technologies
Investing in new technologies is essential to increase productivity in rotomolding. It is important to study the processes and invest in the right technology for the desired work type.
High-performance equipment and automated systems can help increase production, resulting in higher quality and lower cost for the product. These systems can include machines for mass production units as well as more customized and flexible production systems.
Furthermore, modern tools such as sensors and production control and monitoring systems can enhance the efficiency of the rotomolding process. Such tools allow operators to continuously monitor temperature pressure levels, as well as product quality, resulting in better outcomes and maximum productivity.
In this way, we conclude that there are several ways to increase productivity in rotomolding. Selecting the appropriate machine, optimizing cycle time, automating the process, efficient production management, preventive maintenance, quality monitoring and control, team training and development, data analysis, product design, and investment in new technologies are all essential aspects to enhance results in rotomolding. By employing these practices, companies can significantly improve productivity, minimize waste, and maximize profits, bringing important benefits to the organization.